How Metallic Coatings Can Be Applied:
Metallic Coatings may be applied by any one of the following methods.
- Hot Dipping.
- Electroplating and Electroless Plating.
- Metal Spraying.
- Metal Cladding.
- Cementation or Diffusion Coatings.
Hot Dipping- In this process, the metal to be coated is dipped in a molten bath of the coating metal for a sufficient time and then removed out along with the coated film. For example, the process of providing zinc coating on iron is called galvanizing and providing tin (Sn) coating is called tinning.
Metal Spraying- In this process, the coating metal like Al, Zn, etc. in the molten state is sprayed on the surface of the base metal by spraying a gun or pistol. The sprayed metallic coatings are somewhat more porous than those obtained by other processes.
One of the great advantages of this process is that this can be applied to finished structures such as bridges, tanks, ships, towers, etc.
Metal Cladding- It is the process by which a dense, homogeneous, layer of coating metal is bonded firmly and permanently to the base metal on one or both sides.
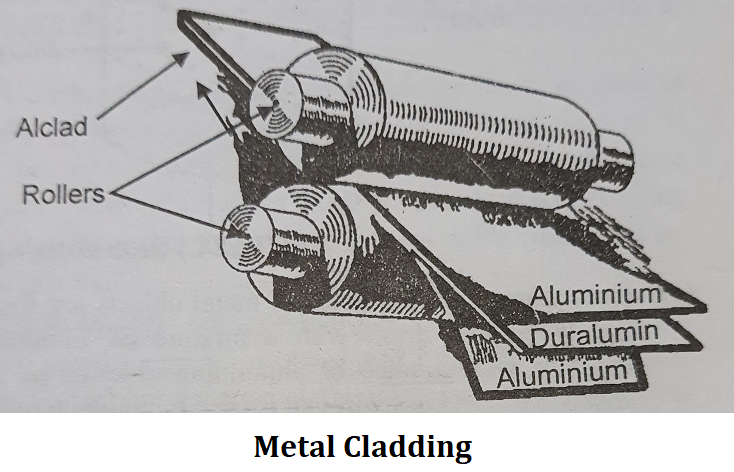
The choice of cladding material depends on the corrosion resistance required for any particular environment. For example, Ni, Cu, Pb, Ag, and alloys like stainless steel copper alloys, and nickel alloys can be commonly used as cladding material.
General cladding is done by arranging thin sheets of coating metal and base metal in the form of a sandwich, which is then passed through rollers under the action of heat and pressure.
For example, a plate of duralumin is sandwiched between two layers of pure aluminium to form ‘alclad’ which is used in the aircraft industry.
Cementation or Diffusion Coating- In this process the coatings are obtained by heating the base metal in a revolving drum containing a powder of the coating metal. The coating metal diffuses into the base metal, resulting in the formation of layers of an alloy of varying composition. The process is suitable for coating small articles of uneven surfaces like bolts, screws, valves, etc. The common coating metals are Zn, Cr, and Al.
Cementation has the following types:
- Sherardizing.
- Colorizing.
- Chromizing.
Sherardizing- In this process of cementation, zinc powder is used as a coating metal. The iron articles to be coated are first cleaned and then packed with zinc dust in a drum. The drum is then sealed tightly so that oxidation of zinc is minimum. The drum is slowly rotated and the temperature is kept at 350℃ to 370℃. During the process, zinc gets diffused into iron to form Fe-Zn alloy at the surface. At the end of the process, the surface of the articles becomes covered with a thin film of iron-zinc alloy.
Applications- This process is usually used for small steel articles like bolts, screws, nuts, etc. The main advantage of the process is that the coating is quite uniform, even if the surface has depression.
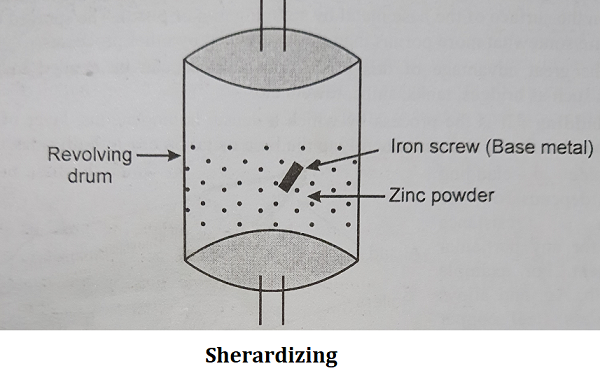
Colorizing- In this case, the metal objects are first sandblasted and then heated in a tightly packed drum with a mixture of aluminum powder and aluminum oxide together with a trace of aluminum chloride as a flux. The process takes place in the absence of air, but hydrogen is used to maintain a reducing atmosphere.
Chromizing- In this case, a mixture of 55% Cr powder and 45% alumina is used as a coating material which is heated with the base metal parts at about 1300℃-1400℃ for 3-4 hours.
The chromizing process is frequently used for the protection of gas turbine blades.
Comments (No)